Selecting the proper process valve for your industrial application is crucial for ensuring efficient, safe, and cost-effective operation.
The process involves understanding the specific requirements of your application, the types of process valves & flow control available, and the materials and technologies that best suit your needs. This comprehensive guide will walk you through the essential considerations and steps to make an informed decision.
Understanding Process Valves
Process valves are mechanical devices that control the flow and pressure of liquids, gases, and slurries within a piping system. They are integral to various industries, including oil and gas, chemical processing, power generation, water treatment, pharmaceuticals, and food and beverage production. The primary functions of process valves include starting and stopping flow, regulating flow and pressure, preventing backflow, and controlling flow direction.
Types of Process Valves
There are several types of process valves, each designed for specific applications and operational conditions. The most common types include:
Gate Valves
Gate valves are used to start or stop the flow of liquid. They operate by lifting a rectangular or circular gate out of the path of the fluid. Gate valves are ideal for applications requiring minimal pressure drop and uninterrupted flow.
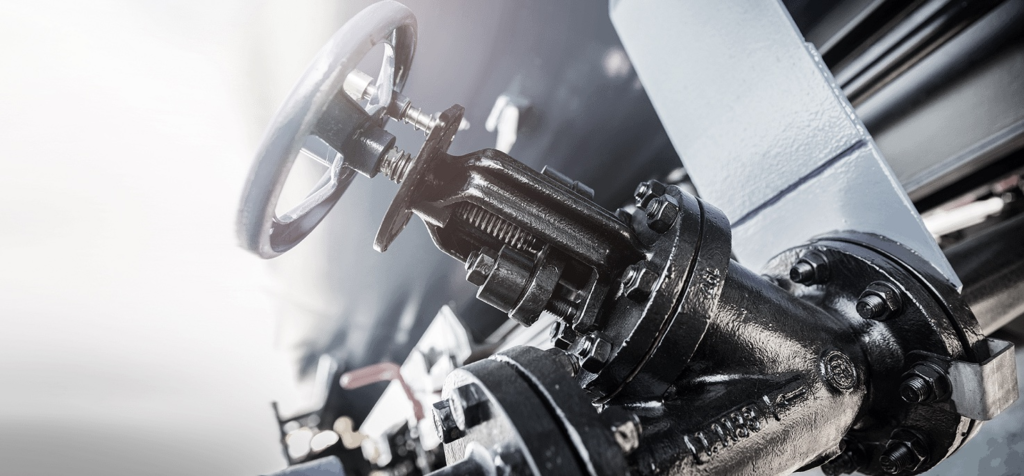
Globe Valves
Globe valves regulate flow in a pipeline. They consist of a movable disk and a stationary ring seat and are suitable for applications where precise flow control is needed.
Ball Valves
Ball valves use a spherical disc to control flow. They are known for their durability and reliability, providing tight shutoff and quick operation. Ball valves are commonly used in applications requiring a quick shut-off mechanism.
Butterfly Valves
Butterfly valves use a rotating disc to regulate flow. They are lightweight, cost-effective, and suitable for large-volume applications. Butterfly valves are commonly used in the water treatment and chemical processing industries.
Check Valves
Check valves allow fluid to flow in one direction only, preventing backflow. They are essential for protecting equipment from damage due to reverse flow and are used in various applications, including water, oil, and gas systems.
Diaphragm Valves
Diaphragm valves use a flexible diaphragm to regulate flow. They are ideal for handling corrosive or abrasive fluids and are commonly used in the pharmaceutical and food industries.
Plug Valves
Plug valves use a cylindrical or conically tapered plug to control flow. They are known for their simple design and reliability, making them suitable for applications requiring frequent operation.
Key Factors to Consider
Fluid Characteristics
The type of fluid being transported through the valve is a critical factor. Consider the following fluid characteristics:
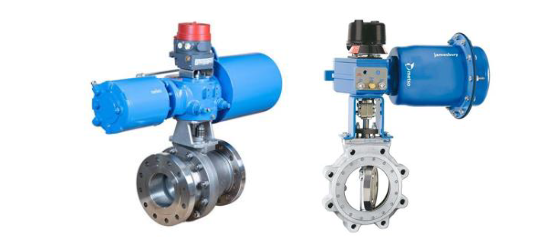
- Type: Identify whether the fluid is a liquid, gas, or slurry.
- Temperature: Ensure the valve material can withstand the operating temperature range.
- Pressure: The valve must be rated for the system’s pressure requirements.
- Viscosity: High-viscosity fluids require valves designed to handle thick, sticky substances.
- Corrosiveness: Corrosive fluids necessitate valves made from corrosion-resistant materials.
- Abrasiveness: Abrasive fluids require valves with durable, wear-resistant materials.
Valve Function
Determine the primary function of the valve in your system:
- On/Off Control: Gate valves and ball valves are ideal for this function.
- Flow Regulation: Globe valves and butterfly valves provide precise control.
- Preventing Backflow: Check valves are designed specifically for this purpose.
- Directional Control: Multi-port valves, such as plug valves, can control the flow direction.
Material Compatibility
Selecting the right material for the valve body, seat, and internal components ensures longevity and performance. Common materials include:
- Metals: Stainless steel, carbon steel, brass, and bronze are used for their strength and durability.
- Plastics: PVC, CPVC, and PTFE are used for their chemical resistance and lightweight properties.
- Elastomers: Materials like EPDM, Viton, and Buna-N are used for their flexibility and sealing capabilities.
Valve Size
The valve size must match the pipeline size to ensure proper flow and pressure management. Consider the following:
- Nominal Pipe Size (NPS): Ensure the valve matches the pipeline diameter.
- Flow Coefficient (Cv): This value indicates the valve’s capacity to allow fluid flow. Ensure the valve’s Cv rating meets your system’s requirements.
Operating Conditions
Evaluate the environmental conditions where the valve will be installed:
- Temperature Extremes: High or low temperatures require valves with appropriate temperature ratings.
- Pressure Variations: Ensure the valve can handle pressure fluctuations.
- Environmental Factors: Consider factors like humidity, chemical exposure, and outdoor installation.
Actuation Method
Valves can be operated manually, pneumatically, electrically, or hydraulically. Choose an actuation method based on:
- Automation Needs: Automated systems often use electric or pneumatic actuators.
- Manual Operation: Simple systems or backup controls may use manual actuation.
- Response Time: Consider how quickly the valve needs to respond to control signals.
Maintenance and Reliability
Consider the maintenance requirements and reliability of the valve:
- Ease of Maintenance: Valves with simple designs and fewer moving parts are easier to maintain.
- Reliability: Choose valves from reputable manufacturers known for their quality and durability.
- Spare Parts Availability: Ensure that replacement parts are readily available.
Steps to Select the Right Process Valve
Define the Application Requirements
Clearly define the application requirements, including the type of fluid, pressure, temperature, and flow characteristics. Document the specific operational needs and any regulatory requirements.
Identify Suitable Valve Types
Based on the application requirements, identify the types of valves suitable for the application. Consider the advantages and disadvantages of each valve type in relation to your system’s specific needs.
Evaluate Material Compatibility
Ensure the materials used in the valve are compatible with the fluid and environmental conditions. Consider factors like corrosion resistance, temperature tolerance, and mechanical strength.
Determine the Valve Size
Calculate the appropriate valve size based on the pipeline diameter and the required flow coefficient (Cv). Ensure the valve size matches the system’s flow and pressure requirements.
Select the Actuation Method
Choose an actuation method that aligns with your system’s control needs. Consider factors like automation, manual operation, and response time.
Consider Maintenance and Reliability
Evaluate the valve’s maintenance requirements and reliability. Choose valves that are easy to maintain and have a proven track record of reliability.
Check Compliance with Standards
Ensure the valve complies with relevant industry standards and certifications. This ensures the valve meets safety, quality, and performance criteria.
Consult with Experts
Consult with valve manufacturers and industry experts to validate your selection. They can provide insights into the best options for your specific application and help you avoid potential pitfalls.
Perform Testing and Validation
Perform testing and validation before full-scale implementation to ensure the selected valve meets all operational requirements. This can include prototype testing, pilot installations, and performance validation under actual operating conditions.
Review and Optimize
Continuously review the valve’s performance in your system and make any necessary adjustments. This ensures optimal performance and longevity.
Conclusion
Selecting the right process valve for your industrial application is a critical decision that impacts the efficiency, safety, and cost-effectiveness of your operations. By understanding the different types of valves, evaluating key factors such as fluid characteristics, material compatibility, and operating conditions, and following a structured selection process, you can make an informed decision that meets your specific needs. Remember to consult with experts, ensure compliance with industry standards, and perform thorough testing to validate your choice. With the right process valve, you can achieve reliable and efficient control of fluid flow in your industrial systems.