In modern manufacturing, quality control is king.
Two primary inspection methods dominate the field: automated AI visual inspection and manual inspection.
While traditional manual inspection has been the backbone of quality assurance for decades, automated AI visual inspection technologies are rapidly changing the game.
We’ll examine both approaches, exploring their strengths, limitations, and real-world applications across various industries. We’ll then unpack how these methods impact accuracy, efficiency, and cost-effectiveness in today’s competitive manufacturing landscape.
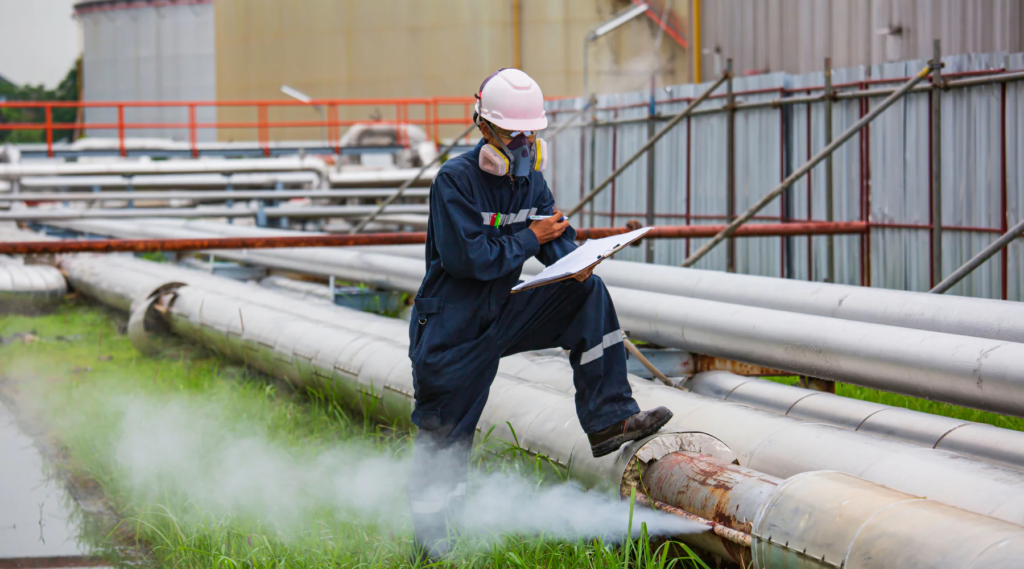
Key Notes
- Automated AI visual inspection outperforms manual methods in accuracy, consistency, and speed across various manufacturing industries.
- AI-powered systems can detect microscopic defects, predict process drift, and enable real-time adjustments to maintain quality.
- While initial investment is high, long-term benefits include reduced labor costs, improved efficiency, and enhanced data analysis capabilities.
- Integration with other smart manufacturing technologies promises even more sophisticated quality control systems in the future.
What Is Automated AI Visual Inspection in Manufacturing?
Automated AI Visual inspection in manufacturing leverages advanced technologies such as machine vision systems, artificial intelligence (AI), and computer vision to detect defects and ensure product quality.
This method has gained significant traction across various industries, including semiconductor manufacturing, automotive production, and pharmaceuticals.
Key Components of Visual Inspection Systems Include:
- High-resolution cameras
- Specialized lighting systems
- Image processing software
- Machine learning algorithms for defect detection
These systems can identify various defects, from microscopic flaws in semiconductor chips to surface imperfections in automotive parts.
Manual Inspection: The Traditional Approach
Manual inspection relies on human operators to visually examine products for defects and has been the backbone of quality control in manufacturing for decades. Inspectors use their expertise, often aided by magnification tools or specialized lighting, to identify and categorize defects.
While manual inspection has merits, such as the ability to make nuanced judgments and adapt quickly to new defect types, it also has significant limitations.
Automated AI Visual Inspection vs. Manual Inspection
Accuracy and Reliability
Automated AI visual inspection systems consistently outperform manual methods in accuracy. In some applications, these systems can detect defects with precision rates exceeding 99%.
Throughput and Productivity
Automated AI visual inspection systems can process hundreds of items per minute, far surpassing the capabilities of human inspectors. This high-speed inspection allows for 100% product coverage without slowing down production lines.
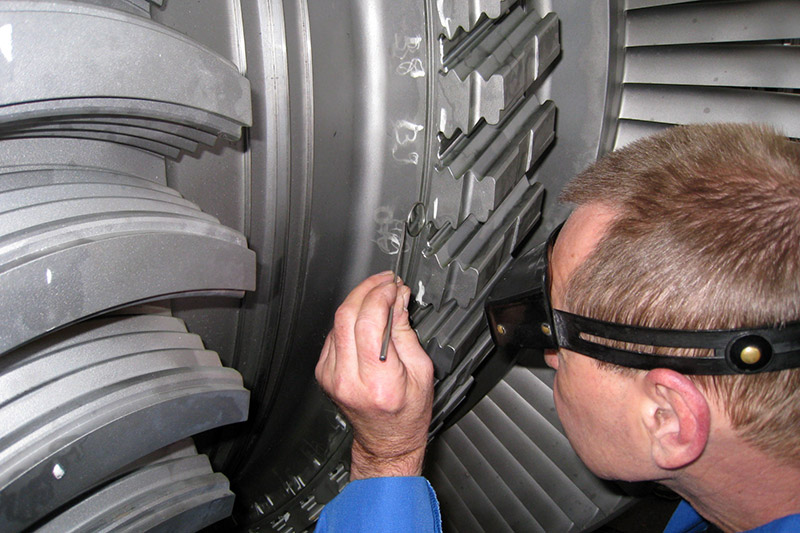
Consistency
One of the primary advantages of automated AI visual inspection is its consistency. Unlike human inspectors, who may experience fatigue or distraction, automated systems maintain the same level of scrutiny throughout extended production runs.
Cost-Effectiveness
While the initial investment in automated AI visual inspection technology can be substantial, the long-term benefits often outweigh the costs.
Reduced labor requirements, decreased quality issues, and improved production efficiency contribute to a favorable return on investment.
Accessibility and Coverage
Automated AI visual inspection systems can access and analyze difficult or impossible areas for human inspectors to see. This means that no potential defects are overlooked due to physical limitations.
Data Collection and Analysis
Automated systems excel in collecting and analyzing inspection data. This wealth of information can be used to identify trends, optimize processes, and prevent future defects, contributing to continuous improvement in manufacturing quality.
Predicting and Preventing Process Drift
An essential aspect of maintaining manufacturing quality is the ability to predict and prevent process drift. Process drift refers to gradual, unintended deviations in manufacturing parameters that can lead to quality issues over time.
Automated AI visual inspection systems play a crucial role in this area by:
- Continuous Monitoring: AI-powered visual inspection systems can detect subtle changes in product characteristics that may indicate the onset of process drift.
- Statistical Process Control (SPC): By integrating visual inspection data with SPC tools, manufacturers can identify trends and patterns that signal potential drift before it impacts product quality.
- Predictive Maintenance: Advanced visual inspection systems can monitor equipment conditions, predicting potential failures that could lead to process drift.
- Real-Time Adjustments: When integrated with manufacturing execution systems, automated AI visual inspection can trigger automatic adjustments to process parameters, maintaining optimal production conditions.
Applications Across Industries
Semiconductor Manufacturing
Visual inspection and AI have become indispensable in the semiconductor industry, where precision is critical. These systems can detect defects as small as a few nanometers, ensuring the quality and reliability of microchips.
Automotive Manufacturing
Automated AI visual inspection systems in automotive production lines can inspect everything from paint quality to the precise alignment of components, significantly reducing the risk of defects in finished vehicles.
Pharmaceutical Production
In pharma manufacturing, automated AI visual inspection ensures the integrity of medicines and packaging, meets stringent regulatory requirements, and safeguards public health.
Food and Beverage Industry
Automated AI visual inspection in food processing can detect foreign objects, ensure proper packaging, and verify label accuracy at high speeds, enhancing safety and efficiency.
Challenges and Considerations
While visual inspection offers numerous advantages, it’s not without challenges:
- Initial Investment: The upfront cost of implementing advanced visual inspection systems can be significant, requiring careful cost-benefit analysis.
- Complexity: Setting up and fine-tuning visual inspection systems often requires specialized expertise.
- Adaptability: While AI systems can learn and adapt, they may need retraining when new product types or defect categories are introduced.
- Data Management: The large volume of data generated by automated AI visual inspection systems necessitates robust data management and analysis capabilities.
Conclusion
As manufacturing processes grow more complex and quality standards rise, automated AI visual inspection is becoming essential. These systems offer superior accuracy, consistency, and efficiency compared to manual methods.
The future of quality control in manufacturing is clearly moving towards automation. Visual inspection technologies enhance product quality and contribute to overall efficiency, helping manufacturers remain competitive in the global market.
Looking ahead, integrating visual inspection with other smart manufacturing technologies will likely lead to even more sophisticated quality control systems, further solidifying its importance in modern production processes.